获评“中国标杆智能工厂”,蜂巢易创引领汽车零部件业数字化转型


近年来,随着工业4.0时代的纵深推进,云计算、智能工业机器人、物联网等新一轮信息技术已逐步在全球各制造业生产过程中得到广泛应用,尤其对于中国汽车制造业来说,随着生产装备的智能化升级和工艺流程的不断改进,“智能工厂”作为工业4.0概念的重要抓手之一,正在引领优势企业通过大数据整合自身产品全生命周期研发,加速向智能化、数字化及服务化转型。
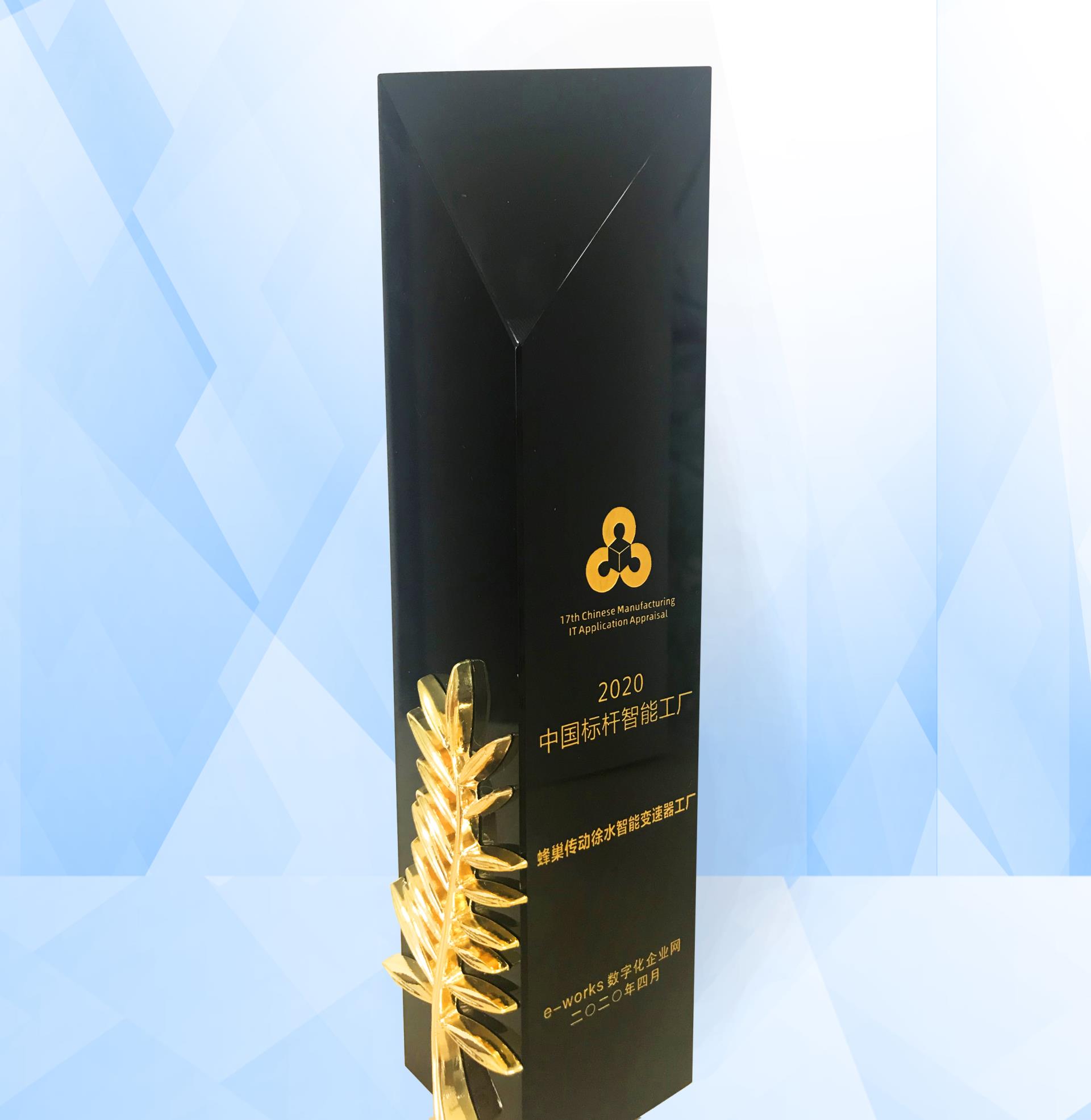
工厂整体建设均对标国际化标准,以高度灵活的个性化和数字化产品与服务生产模式为核心目标,引进国际先进的生产设备和智能制造工艺,如:采用微正压设计通过集中吸雾、集中冷却等技术保证工作环境的可控性,轴、齿等采用低压渗碳、激光焊接等先进工艺配合高端精密设备,实现产品质量的高度一致性。

目前,工厂整体已从建设智能物流、智能热处理、智能装配、智能测试系统,建设生产及信息化,建立工厂数据中心和互联互通网络等四大部分实现了数字化、智能化。值得注意的是,该智能工厂生产的7DCT变速器产品自2017年量产上市以来,曾多次斩获行业诸多重量级奖项,诸如“世界十佳变速器”、中国汽车工业科学技术进步奖“一等奖、国际汽车技术年会”创新开发项目大奖”等,截至2020年3月产销量已累计突破130万台,显示出良好的发展前景。
蜂巢易创基于创新的产品研发设计和智能的生产工艺,陆续通过IATF16949:2016、ISO9001:2015等质量管理体系认证,并依托全自动化、智能化的先进生产优势,先后陆续发布了“I纪元”、“ 扁时代”、“ DP-EPS”等产品技术品牌规划,包含传统动力形式、混动和电动化多重技术路线,在中国汽车零部件行业逐渐展露锋芒。
除此之外,蜂巢易创斥巨资在江苏扬中汽车零部件产业园打造的涵盖产品研发、功能研发、综合验证、工艺研发及智能制造技术开发为一体的“智慧工厂”,也即将于2020年年底投入生产,并将继续以工业服务网和工业物联网为基本框架,以工业4.0智能制造信息化技术开发及品质管理技术(SQE等)、产品技术(EOL、售后等)、制造技术(自动化、数字化、工艺开发等)等智能开发支持为核心内容,加强对新模式、新业态、新平台的研究,创新建立更智能、更高效、更安全、更具可持续性的新一代智能制造生态系统,以助推中国制造真正实现“工业4.0”。
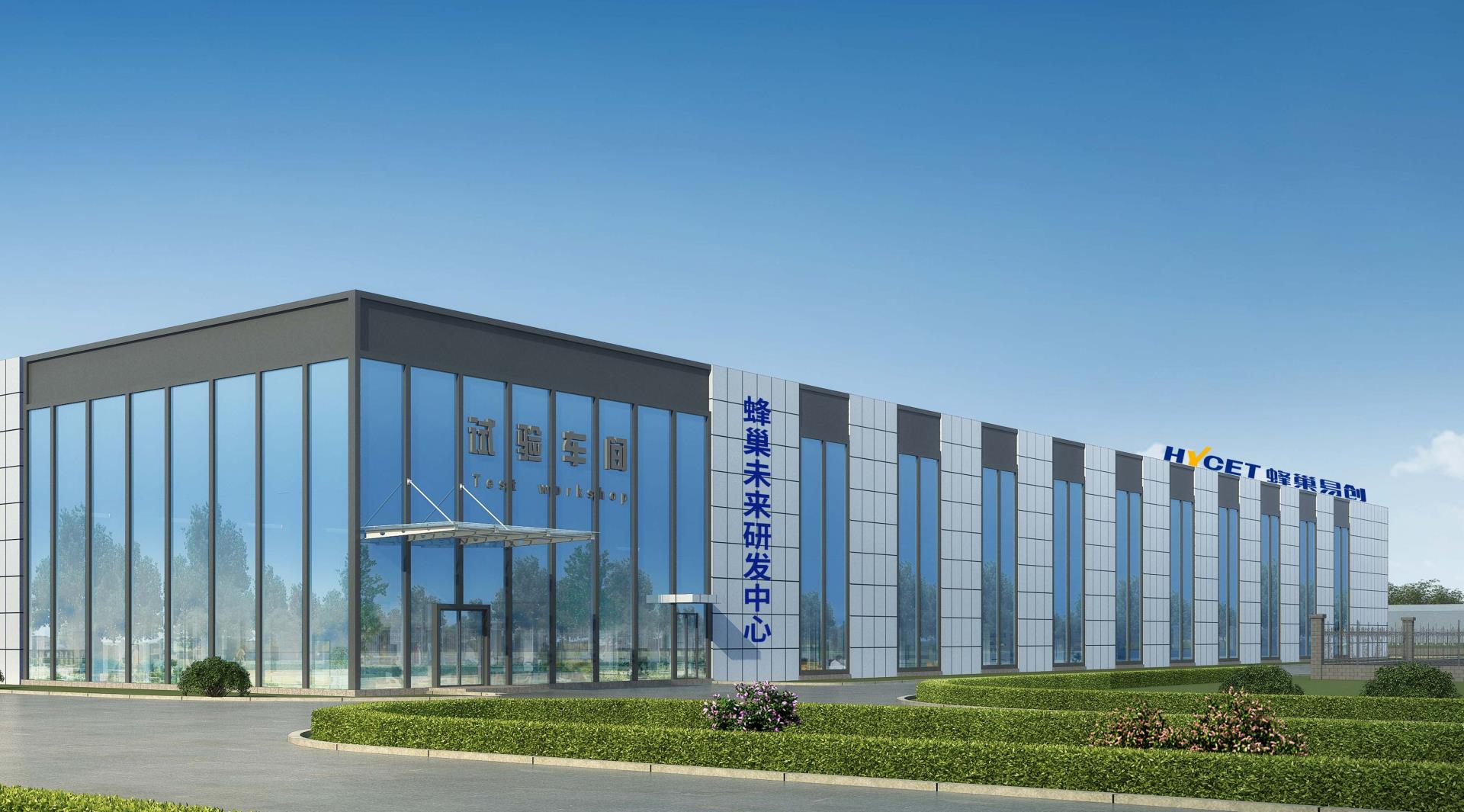
善进者,无止境。横向扩展产品线和生产工厂布局,纵向深耕产品研发设计和生产线智能优化,基于这一战略导向,蜂巢易创积极探索新形势下的发展思路从未停止过,仍在通过不断的创新和优化运营机制,来提升自主品牌核心竞争力,并依靠科技创新、智能制造转型和多元化联动发展模式,大步迈出了数字化转型、高质量发展的创新路子。
5月22日晚,由中国智能制造领域专业媒体——e-works数字企业网组织评选的“2020中国标杆智能工厂”榜单揭晓,蜂巢易创徐水智能变速器工厂成功入选,成为中国汽车零部件制造业智能化、数字化转型的标杆之一。
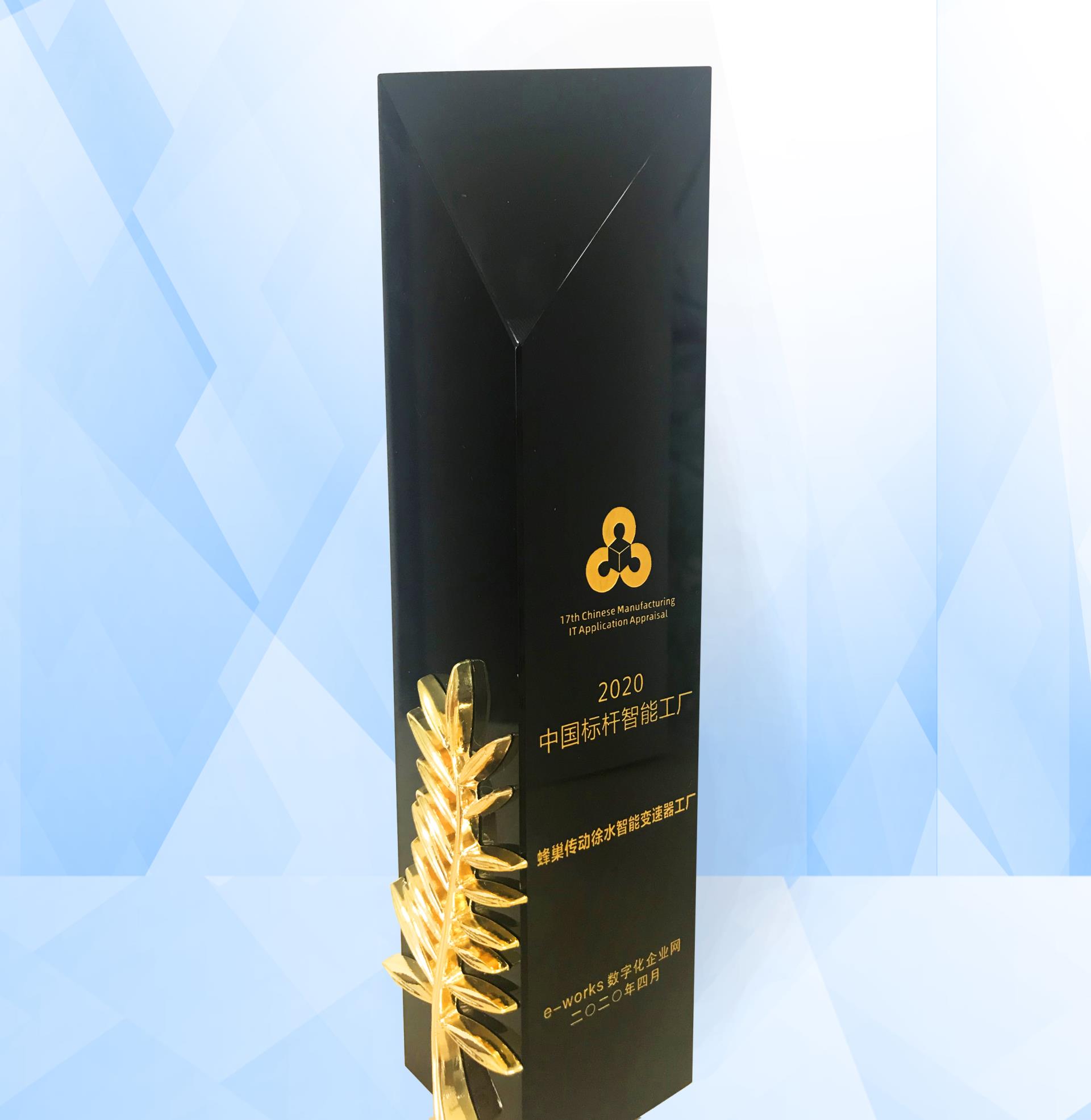
据蜂巢易创科技有限公司相关负责人介绍,蜂巢易创徐水智能变速器工厂能够在今年上百家参评的优秀企业中脱颖而出,正是得益于其始终坚持“智能、绿色、创新”理念,深耕智能制造生产技术,顺应智能化、数字化时代的前瞻性优势。
据了解,该工厂于2015年在河北徐水经济开发区汽车整车及零部件产业园开工建设,2017年正式投产,总占地面积14.5万㎡,总投资33亿元,员工1500余人,具备年产100 万台的生产能力。
自建设之初,该工厂就被定位为“智能工厂”,并通过应用大数据、物联网等创新信息技术,借助产品个性化、装备智能化、生产自动化、管理网络化等,推进制造模式向个性制造、协同制造、柔性制造和绿色制造不断转型。
据了解,该工厂于2015年在河北徐水经济开发区汽车整车及零部件产业园开工建设,2017年正式投产,总占地面积14.5万㎡,总投资33亿元,员工1500余人,具备年产100 万台的生产能力。
自建设之初,该工厂就被定位为“智能工厂”,并通过应用大数据、物联网等创新信息技术,借助产品个性化、装备智能化、生产自动化、管理网络化等,推进制造模式向个性制造、协同制造、柔性制造和绿色制造不断转型。

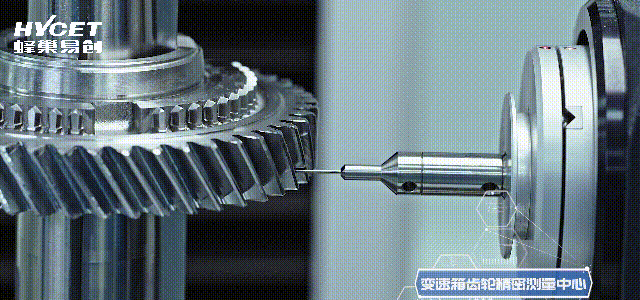
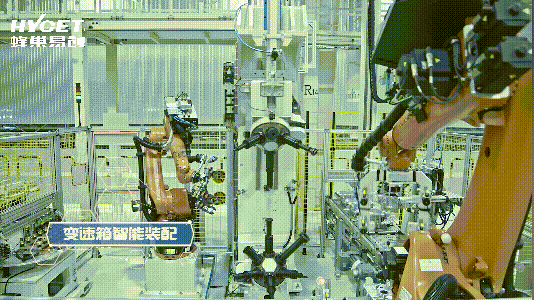

同时,装配线引进大量机器人、数字化工具、全自动无人化生产及检测等先进设备,使整体综合效率提升到300%以上,减少操作人员60%以上,整线防错率达到100%,质量全面监控合格率达到99.79%的优秀水准,有效保证产品的一致性、可靠性。
除此之外,该工厂也对变速器生产过程中的典型工艺进行了自动化、智能化改造。特别是在推进物流自动化和信息化方面,通过引进工厂智能物流信息管理系统,建立壳体智能立体仓库,已逐步实现系统自动识别、自动检测、自动分拣、自动存取、自动跟踪等多种无人化管理功能,使物流相关作业快速、精准、可靠地完成。

智慧物流
目前,工厂整体已从建设智能物流、智能热处理、智能装配、智能测试系统,建设生产及信息化,建立工厂数据中心和互联互通网络等四大部分实现了数字化、智能化。值得注意的是,该智能工厂生产的7DCT变速器产品自2017年量产上市以来,曾多次斩获行业诸多重量级奖项,诸如“世界十佳变速器”、中国汽车工业科学技术进步奖“一等奖、国际汽车技术年会”创新开发项目大奖”等,截至2020年3月产销量已累计突破130万台,显示出良好的发展前景。
蜂巢易创基于创新的产品研发设计和智能的生产工艺,陆续通过IATF16949:2016、ISO9001:2015等质量管理体系认证,并依托全自动化、智能化的先进生产优势,先后陆续发布了“I纪元”、“ 扁时代”、“ DP-EPS”等产品技术品牌规划,包含传统动力形式、混动和电动化多重技术路线,在中国汽车零部件行业逐渐展露锋芒。
除此之外,蜂巢易创斥巨资在江苏扬中汽车零部件产业园打造的涵盖产品研发、功能研发、综合验证、工艺研发及智能制造技术开发为一体的“智慧工厂”,也即将于2020年年底投入生产,并将继续以工业服务网和工业物联网为基本框架,以工业4.0智能制造信息化技术开发及品质管理技术(SQE等)、产品技术(EOL、售后等)、制造技术(自动化、数字化、工艺开发等)等智能开发支持为核心内容,加强对新模式、新业态、新平台的研究,创新建立更智能、更高效、更安全、更具可持续性的新一代智能制造生态系统,以助推中国制造真正实现“工业4.0”。
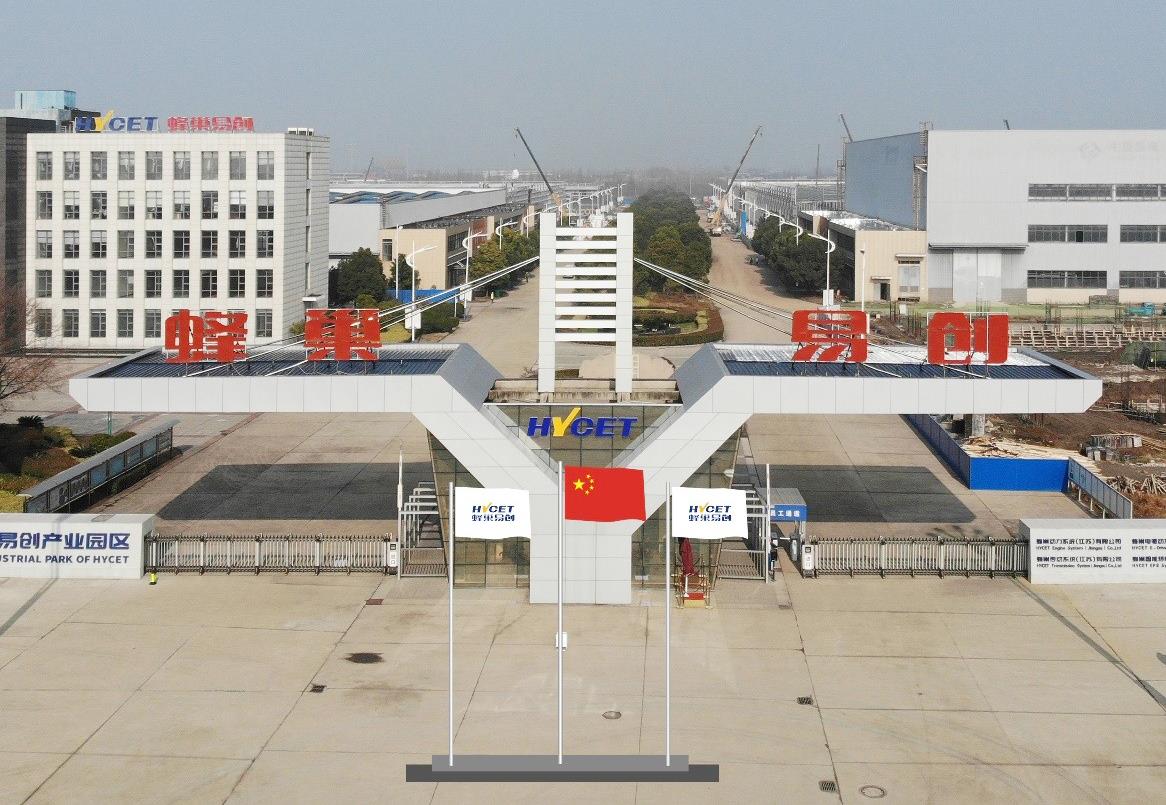
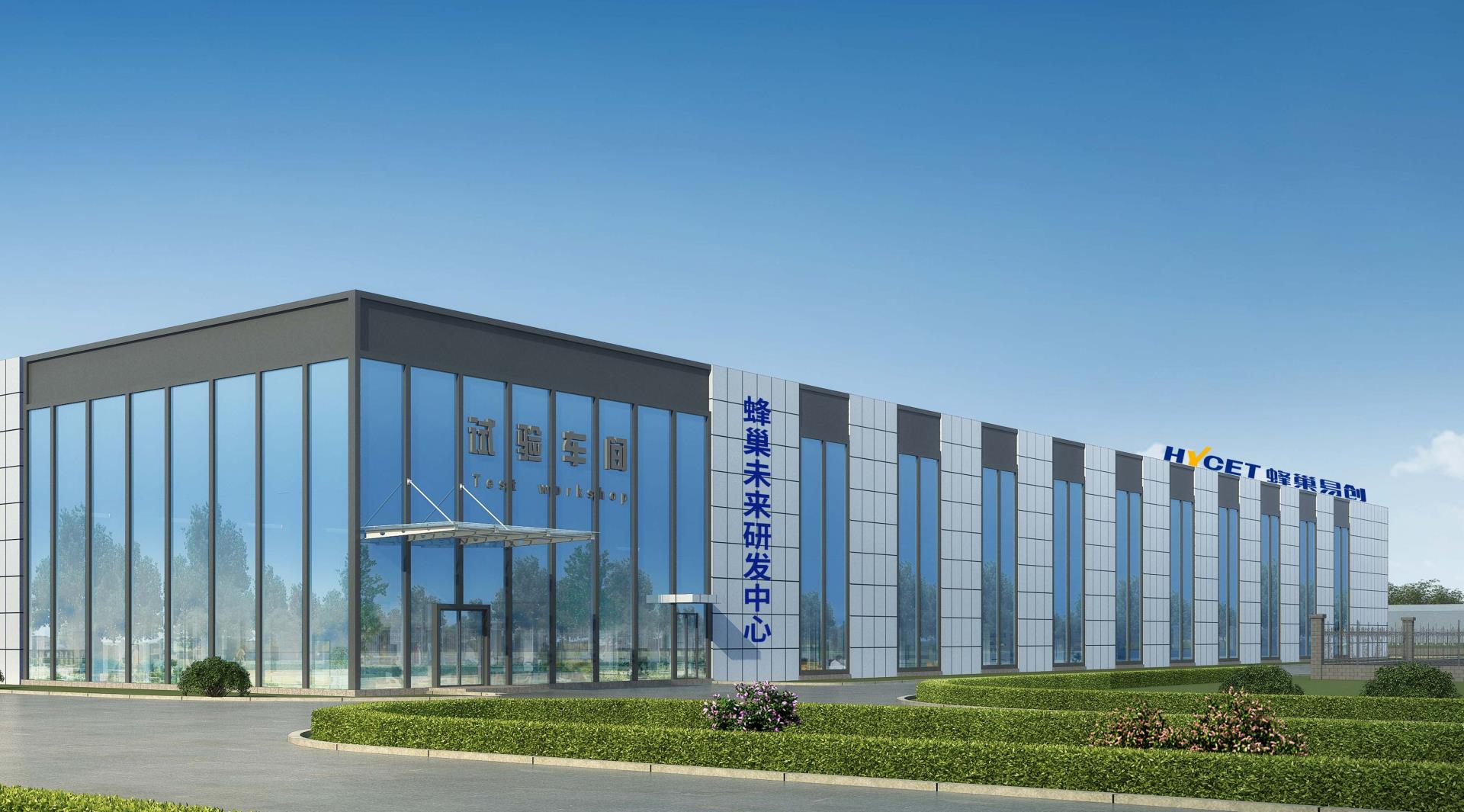
蜂巢易创扬中产业园研发试验中心效果图
善进者,无止境。横向扩展产品线和生产工厂布局,纵向深耕产品研发设计和生产线智能优化,基于这一战略导向,蜂巢易创积极探索新形势下的发展思路从未停止过,仍在通过不断的创新和优化运营机制,来提升自主品牌核心竞争力,并依靠科技创新、智能制造转型和多元化联动发展模式,大步迈出了数字化转型、高质量发展的创新路子。